As an Amazon Associate, I earn from qualifying purchases.
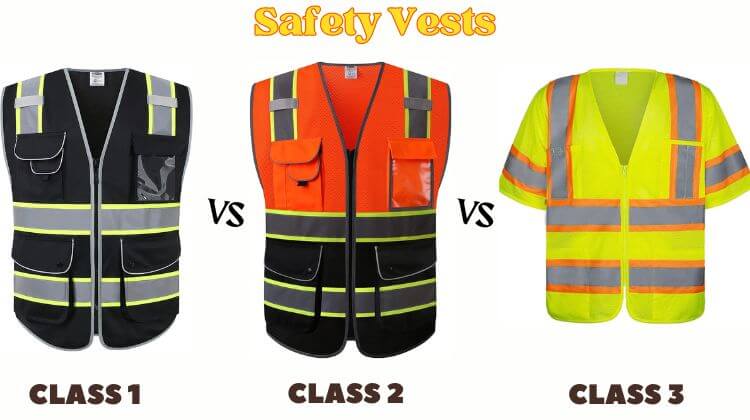
Safety vests play a crucial role in enhancing visibility and reducing accidents to ensure safety in various work environments. However, safety vests are not a one-size-fits-all solution. They are categorized into classes based on their reflective properties and visibility levels. In this article, we will demystify Class 1, 2, and 3 safety vests, shedding light on their key differences and helping you make an informed choice when selecting the correct safety vest for your needs.
Importance of Safety Vests
Protective safety vests are crucial equipment that helps workers become more visible in dangerous work environments. They are widely used in construction sites, roadwork, traffic control, and other industries where visibility is critical for worker safety. Workers can decrease their chances of accidents and injuries by wearing safety vests, which make them more visible to drivers, machine operators, and other workers.
High Visibility Clothing Class 1 2 3:
To maintain consistent levels of visibility and performance, safety vests are required to adhere to the guidelines and standards set by the American National Standards Institute (ANSI) and the International Safety Equipment Association (ISEA). These standards categorize safety vests into three classes: Class 1, Class 2, and Class 3.
3.1 Class 1 Safety Vests
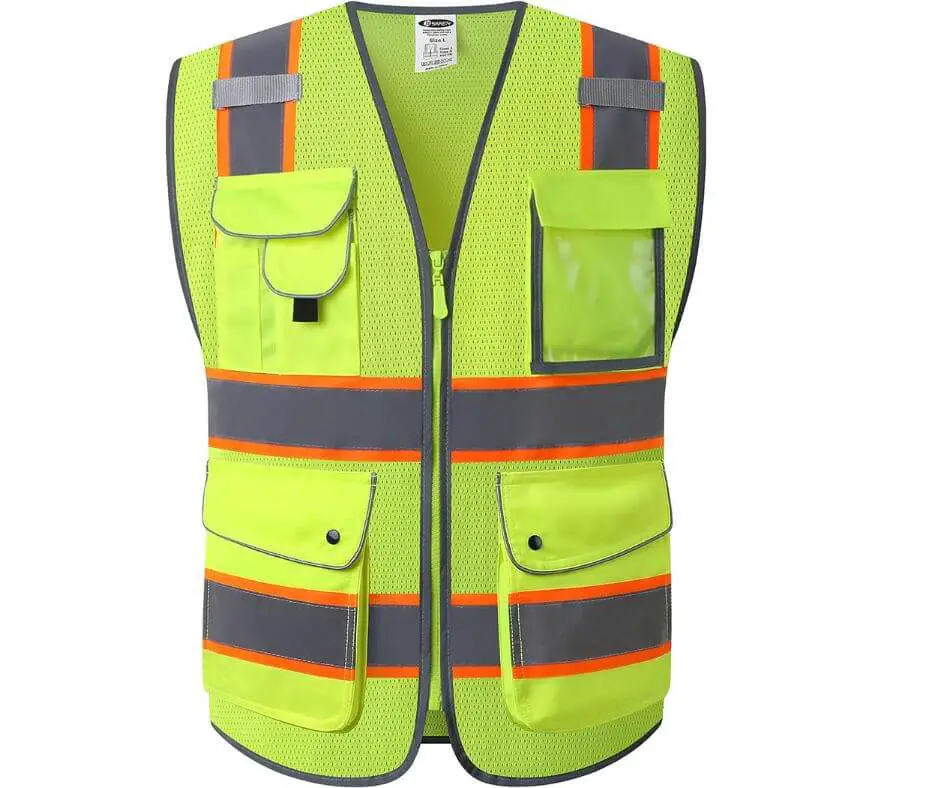
For work environments with low visibility and traffic that does not exceed 25 miles per hour, Class 1 safety vests are the appropriate choice. These vests suit parking attendants, warehouse workers, and sidewalk maintenance personnel. Class 1 safety vests provide the lowest level of visibility among the three classes.
3.2 Class 2 Safety Vests
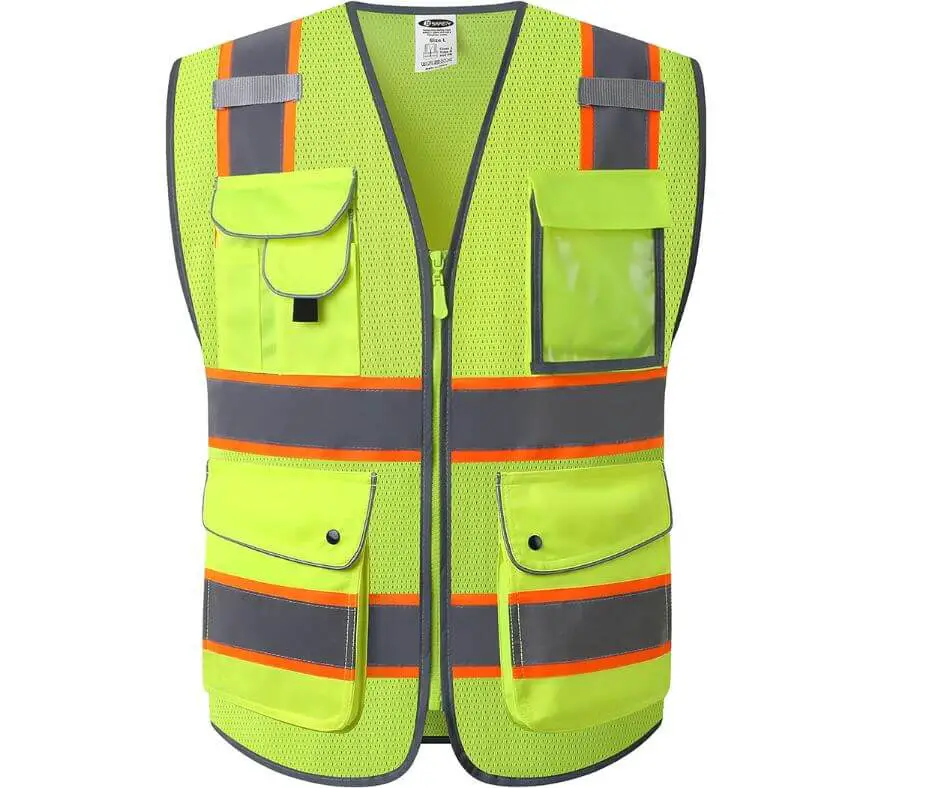
Class 2 safety vests are suitable for work environments with moderate traffic conditions, where speeds range from 25 to 50 miles per hour. Roadway construction workers, surveyors, and utility workers frequently use these vests. Class 2 safety vests offer enhanced visibility compared to Class 1 vests.
3.3 Class 3 Safety Vests
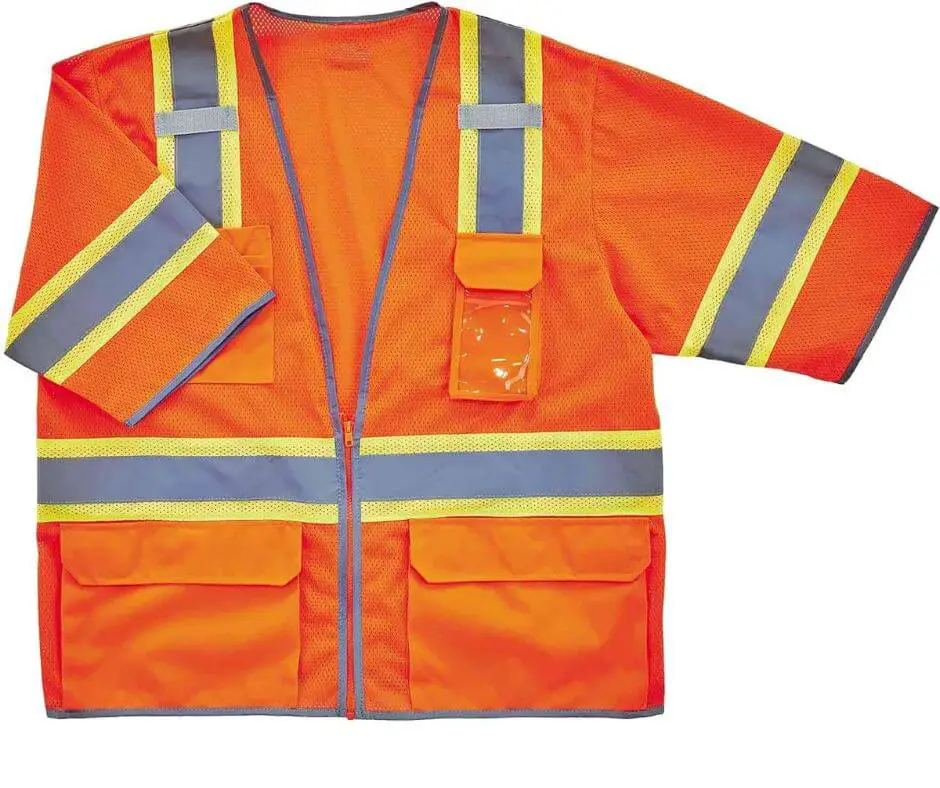
Class 3 safety vests are for high-visibility work areas with heavy traffic over 50 mph. Highway construction workers, emergency responders, and tow truck operators usually wear these vests. Class 3 safety vests provide the highest level of visibility among the three classes.
Requirements for Class 1 Safety Vests
Class 1 safety vests have specific design and reflective material requirements to ensure adequate visibility in low-risk work environments.
4.1 Design and Reflective Material
Vests in Class 1 need to have at least 155 square inches of reflective material., with reflective bands measuring at least 6.46 linear feet. The vest’s background material must be a high-visibility color, such as fluorescent yellow or orange.
4.2 Minimum Visible Background Material
Class 1 safety vests must also have a minimum of 217 square inches of visible background material, which provides a contrast to the reflective bands. This visual background material ensures the vest is easily distinguishable even in low-light conditions.
Class 2 Safety Vest Requirements
Class 2 safety vests have additional requirements to provide enhanced visibility in moderate-risk work environments.
5.1 Enhanced Visibility and Reflective Tape
According to regulations, Class 2 vests are required to have at least 201 square inches of reflective material., with reflective bands measuring at least 8.373 linear feet. These vests often feature reflective tape across the shoulders, around the waist, and the torso area for increased visibility from different angles.
5.2 Minimum Visible Background Material
Like Class 1 vests, Class 2 safety vests must also have a minimum of 775 square inches of visible background material, ensuring the vest stands out even in conditions with limited lighting.
Class 3 Safety Vests Requirements: Maximum Visibility
Class 3 safety vests are necessary for high-risk workplaces, where maximum visibility is crucial.
6.1 Enhanced Visibility and Reflective Tape
For Class 3 vests, a minimum of 310 square inches of reflective material is required, with reflective bands measuring at least 12.92 linear feet. These vests typically feature reflective tape on the sleeves and full 360-degree coverage to ensure visibility from all directions.
6.2 Minimum Visible Background Material
To meet Class 3 standards, safety vests must have a minimum of 1,240 square inches of visible background material. Providing a significant contrast to the reflective bands and maximizing the visibility in any lighting condition.
Choosing the Right Safety Vest
When selecting a safety vest, assessing the specific work environment and considering the level of visibility required is crucial. Here are a few key factors to keep in mind:
- Determine the traffic conditions and speed in the work area.
- Identify the level of risk and visibility needed for the job.
- Select a safety vest that complies with the appropriate ANSI/ISEA standards.
- Consider additional features like pockets, closure types, and breathable materials for convenience and comfort.
It’s important to remember that selecting the appropriate safety vest can significantly promote a secure workplace and avoid mishaps.
Conclusion
In conclusion, safety vests ensure worker visibility and safety in various industries. Class 1, 2, and 3 safety vests are designed to meet different visibility requirements based on the work environment’s risk level. By understanding the critical differences between these classes, we will provide you with all the necessary information to ensure you select the right safety vest for your specific requirements.